HYDRAULIC BRAKE
-
Definition of Hydraulic Brake
The hydraulic brake is an arrangement of braking mechanism which uses brake fluid, typically containing ethylene glycol, to transfer pressure from the controlling mechanism to the braking mechanism.
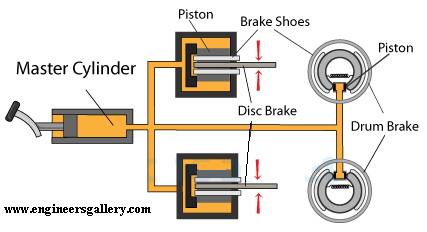
- History
Fred Duesenberg originated hydraulic brakes on his 1914 racing cars and Duesenberg was the first automotive marque to use the technology on a passenger car in 1921. This braking system could have earned him a fortune if he had patented it. In 1918 Malcolm Lougheed (who later changed the spelling of his name to Lockheed) developed a hydraulic brake system.
- Construction
The most common arrangement of hydraulic brakes for passenger vehicles, motorcycles, scooters, and mopeds, consists of the following:
- Brake pedal or lever
- A push-rod (also called an actuating rod)
- A master cylinder assembly containing a piston assembly (made up of either one or two pistons, a return spring, a series of gaskets/ O-rings and a fluid reservoir)
- Reinforced hydraulic lines
- Brake caliper assembly usually consisting of one or two hollow aluminum or chrome-plated steel pistons (called caliper pistons), a set of thermally conductive brake pads and a rotor (also called a brake disc) or drum attached to an axle.
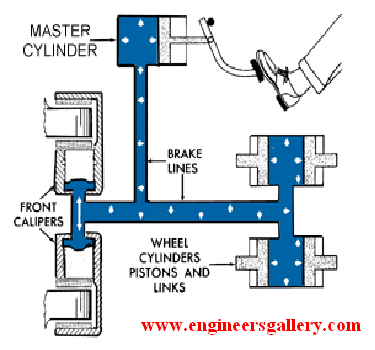
The system is usually filled with a glycol-ether based brake fluid (Other fluids may also be used).
Related Articles
Braking System and Its Classification, Application, Advantages and Disadvantages
At one time, passenger vehicles commonly employed drum brakes on all four wheels. Later, disc brakes were used for the front and drum brakes for the rear. However disc brakes have shown better heat dissipation and greater resistance to ‘fading’ and are therefore generally safer than drum brakes. So four-wheel disc brakes have become increasingly popular, replacing drums on all but the most basic vehicles. Many two-wheel vehicle designs, however, continue to employ a drum brake for the rear wheel.
The following description uses the terminology for and configuration of a simple disc brake.
- Operation of Hydraulic Brake
In a hydraulic brake system, when the brake pedal is pressed, a push-rod exerts force on the piston(s) in the master cylinder, causing fluid from the brake fluid reservoir to flow into a pressure chamber through a compensating port. This results in an increase in the pressure of the entire hydraulic system, forcing fluid through the hydraulic lines toward one or more calipers where it acts upon one or two caliper pistons sealed by one or more seated O-rings (which prevent leakage of the fluid).
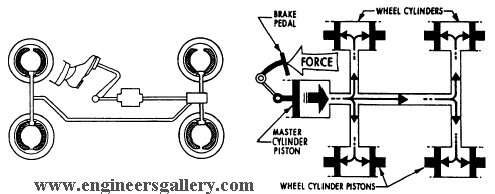
The brake caliper pistons then apply force to the brake pads, pushing them against the spinning rotor, and the friction between the pads and the rotor causes a braking torque to be generated, slowing the vehicle. Heat generated by this friction is either dissipated through vents and channels in the rotor or is conducted through the pads, which are made of specialized heat-tolerant materials such as Kevlar or sintered glass.
Subsequent release of the brake pedal/lever allows the spring(s) in the master cylinder assembly to return the master piston(s) back into position. This action first relieves the hydraulic pressure on the caliper, then applies suction to the brake piston in the caliper assembly, moving it back into its housing and allowing the brake pads to release the rotor.
The hydraulic braking system is designed as a closed system: unless there is a leak in the system, none of the brake fluid enters or leaves it, nor does the fluid get consumed through use.
- An example of a hydraulic brake system
Hydraulic brakes transfer energy to stop an object, normally a rotating axle. In a very simple brake system, with just two cylinders and a disc brake, the cylinders could be connected via tubes, with a piston inside the cylinders. The cylinders and tubes are filled with in compressible oil. The two cylinders have the same volume, but different diameters, and thus different cross-section areas. The one with the smallest diameter is called the master cylinder. The spinning disc brake will be placed down at[clarification needed] the piston with the larger cross-section. Suppose the diameter of the master cylinder is half the diameter of the slave cylinder, so the master cylinder has a cross-section four times smaller. Now, if the piston in the master cylinder is pushed down 40 mm, with 10 newtons (N) of force, the slave piston will then move 10 mm, with a force of 40 N.
This force can be further increased by inserting a lever connected between the master piston, a pedal, and a pivot point. If the distance from the pedal to the pivot is three times the distance from the pivot to the connected piston, then it multiplies the pedal force by a factor of 3, when pushing down on the pedal. Now, if we push the pedal 120 mm down, with 10 N of force, a force of 30 N will then be applied to the master piston, and the slave piston will move the brake pad by 10 mm, with a force of 120 N.
- Advantages
- Hydraulic Brakes are cheaper.
- Hydraulic Brakes are safer.
- Hydraulic Brakes are fast.
- Hydraulic Brakes are greener.
- Hydraulic Brakes are energy efficient.
- Hydraulic Brakes use less standby.
- Hydraulic Brakes stay cool.
- Hydraulic Brakes are powerful.
- Hydraulic Brakes are the best for architects & planners.
- Hydraulic Brakes are better than traction Brakes.
- Hydraulic fluid is highly corrosive to most of the aircraft materials.
- Disadvantages
- Due to the heavy loads experienced in a typical hydraulic system, structural integrity is a must which also means higher structural weight for the aircraft in addition to the weight of its hydraulic lines, pumps, reservoirs, filters, & etc.
- Hydraulic system is susceptible to contamination’s & foreign object damage (FOD).
- Mishandling and constant exposure to hydraulic fluid and its gas fumes without proper equipment and precautions is a health risk.
- If disposed improperly, a hydraulic fluid is an environmental risk.
Reference Wikipedia
Post Comment
You must be logged in to post a comment.