Structural analysis of 3D printed structures-Mechanical Projects
Abstract:
Work will be aimed on investigation of 3D printed beam (honeycomb) structures from the mechanical point of view. In the beginning types of 3D printed structures will be collected (as a source of information, internet should be used (key words: 3D printed structure; honeycomb structure). Finite element method will be used for solving displacement and nominal stress for each structure cell. Results will be used for engineering analysis which will involve volume parameter.
Output of such analysis should be efficiency of used material. Several criteria could be also used (e.g. if the need is to “optimise” the structure on minimum displacement which type of beam topology should be used).
Goals:
– Based on collected 3D cell structures make a parametric models of geometry in Gmesh
- Boundary dimension will be the same for each cell; only cube
- Circular cross section with the same diameter
- Circular cross section with the same volume for cells
– Create workflow Gmsh – Salome meca – Code_Aster
– Engineering optimization
- Criterion (the same diameter of beam cell; the same volume of cell)
- Load structure cells (compression, torsion and shearing) and investigate maximum nominal stress and maximum displacement
- Analyse results
Loading types:
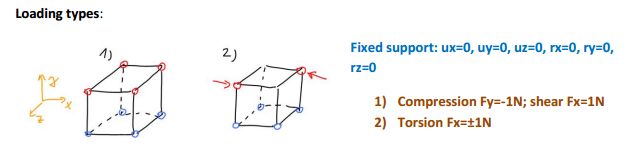
Fixed support: ux=0, uy=0, uz=0, rx=0, ry=0, rz=0
1) Compression Fy=-1N; shear Fx=1N
2) Torsion Fx=±1N
Geometry types: (examples)
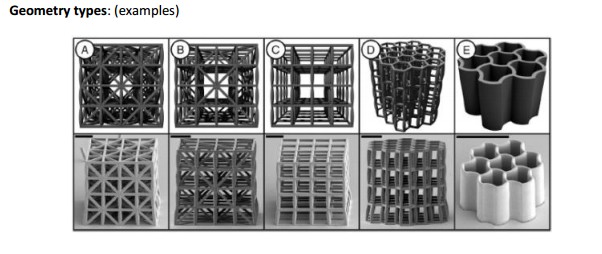
Output of the study:
– Data sources (files *.hdf, *.comm; *.geo) for each cell study. System and organization of
variants should be done.
– Study report – short description of computational model (geometric properties – cell dimension, boundary conditions, material parameters; analysis of different 3D structure cells
(tables of results, description of mechanical behaviour of cells and its advantage disadvantage in certain loading/optimization criteria.
Post Comment
You must be logged in to post a comment.