HERRINGBONE GEAR
Herringbone gears, also called double helical gears, are gear sets designed to transmit power through parallel or, less commonly, perpendicular axes. The unique tooth structure of a herringbone gear consists of two adjoining, opposite helixes that appear in the shape of the letter ‘V’.
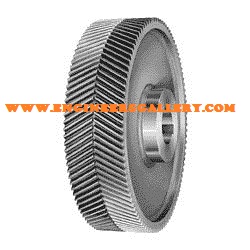
A herringbone gear, a specific type of double helical gear, is a special type of gear which is a side to side (not face to face) combination of two helical gears of opposite hands. From the top the helical grooves of this gear looks like letter V. Unlike helical gears they do not produce an additional axial load.
Herringbone gears mate via the use of smooth, precisely manufactured V-shaped teeth. Like helical gears multiple teeth are engaged during rotation, distributing the work load and offering quiet operation. However, due to their tooth structure, herringbone gears nullify the axial thrust typical of helical gears.
The gear set’s teeth may be manufactured so that tooth-tip aligns with the opposite tooth-tip, or so tooth-tip aligns with the opposite gear’s tooth trough.
Like helical gears, they have the advantage of transferring power smoothly because more than two teeth will be in mesh at any moment in time. Their advantage over the helical gears is that the side-thrust of one half is balanced by that of the other half. This means that herringbone gears can be used in torque gearboxes without requiring a substantial thrust bearing. Because of this herringbone gears were an important step in the introduction of the steam turbine to marine propulsion.
Precision herringbone gears are more difficult to manufacture than equivalent spur or helical gears and consequently are more expensive. They are used in heavy machinery.
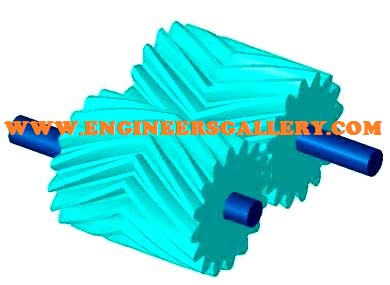
Where the oppositely angled teeth meet in the middle of a herringbone gear, the alignment may be such that tooth tip meets tooth tip, or the alignment may be staggered, so that tooth tip meets tooth trough. The latter alignment is the unique defining characteristic of a Wuest type herringbone gear, named after its inventor.
Herringbone Gear Applications
Application requirements should be considered with the workload and environment of the gear set in mind.
- Power, velocity and torque consistency and output peaks of the gear drive so the gear meets mechanical requirements.
- Operation disruption resistance. It may be necessary for some gear sets to function despite missing teeth or misalignment.
- Mounting requirements. Application may limit the gear’s shaft positioning.
- Precision requirement of gear, including gear pitch, shaft diameter, pressure angle and tooth layout. Herringbone gears’ precise teeth can make them expensive.
- Gear lubrication requirements. Some gears require lubrication for smooth, temperate operation.
- Vibration and shock resistance. Heavy machine loads or backlash, the deliberate surplus space in the circular pitch, may jostle gearing.
- Inertia of the gear through acceleration and deceleration. Heavier gears can be harder to stop or reverse.
- Corrosion resistance. Gears exposed to harsh environments or chemicals should be especially hardened or protected.
- Temperature exposure. Some gears may warp or become brittle in the face of extreme temperatures.
- Noise limitation. Commercial applications may value a smooth, quietly meshing gear. Herringbone gears offer quiet operation.
Post Comment
You must be logged in to post a comment.