HELICAL GEAR
Helical gears are similar to the spur gear except that the teeth are at an angle to the shaft, rather than parallel to it as in a spur gear. The resulting teeth are longer than the teeth on a spur gear of equivalent pitch diameter. The longer teeth cause helical gears to have the following differences from spur gears of the same size:
- Tooth strength is greater because the teeth are longer,
- Greater surface contact on the teeth allows a helical gear to carry more load than a spur gear.
- The longer surface of contact reduces the efficiency of a helical gear relative to a spur gear.
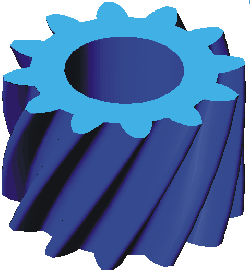
Helical gears may be used to mesh two shafts that are not parallel, although they are still primarily use in parallel shaft applications. A special application in which helical gears are used is a crossed gear mesh, in which the two shafts are perpendicular to each other: The basic descriptive geometry for a helical gear is essentially the same as that of the spur gear, except that the helix angle must be added as a parameter.
Helical or “dry fixed” gears offer a refinement over spur gears. The leading edges of the teeth are not parallel to the axis of rotation, but are set at an angle. Since the gear is curved, this angling causes the tooth shape to be a segment of a helix. Helical gears can be meshed in parallel or crossed orientations. The former refers to when the shafts are parallel to each other; this is the most common orientation. In the latter, the shafts are non-parallel, and in this configuration the gears are sometimes known as “skew gears”.
A disadvantage of helical gears is a resultant thrust along the axis of the gear, which needs to be accommodated by appropriate thrust bearings, and a greater degree of sliding friction between the meshing teeth, often addressed with additives in the lubricant.
- The angled teeth engage more gradually than do spur gear teeth causing them to run more smoothly and quietly
- Helical gears are highly durable and are ideal for high load applications.
- Helical gears can be used on non parallel and even perpendicular shafts, and can carry higher loads than can spur gears.
- At any given time their load is distributed over several teeth, resulting in less wear.
- Can transmit motion and power between either parallel or right angle shafts.
- An obvious disadvantage of the helical gears is a resultant thrust along the axis of the gear, which needs to be accommodated by appropriate thrust bearings, and a greater degree of sliding friction between the meshing teeth, often addressed with additives in the lubricant. Thus we can say that helical gears cause losses due to the unique geometry along the axis of the helical gear’s shaft.
- Efficiency of helical gear is less because helical gear trains have sliding contacts between the teeth which in turns produce axial thrust of gear shafts and generate more heat. So, more power loss and less efficiency.
- Helical gears have the major disadvantage that they are expensive and much more difficult to find.
- Helical gears are also slightly less efficient than a spur gear of the same size.